The dental industry has undergone a transformative shift in the fabrication of prostheses, with dental lab products evolving to meet the demands of precision, efficiency, and patient satisfaction. Two primary methods dominate the landscape: the advanced digital CAD/CAM workflow and the time-tested traditional casting manner. While both approaches produce high-quality prostheses, the digital workflow offers unmatched precision and speed, making it the preferred choice for modern dental labs. This blog post explores both methods, with a focus on the digital CAD/CAM process, and provides structured equipment operation sequences for clarity.
Digital CAD/CAM Workflow: Precision and Efficiency
The digital CAD/CAM workflow has revolutionized prostheses fabrication by integrating cutting-edge technology to streamline processes. This method leverages dental lab products like scanners, software, and milling machines to create prosthetics such as crowns, bridges, and dentures with exceptional accuracy. Below is the step-by-step workflow:
- Desktop Scanner: The process begins with a desktop scanner, which captures detailed 3D images of the patient’s dental structures. This digital model serves as the foundation for the prosthetic design, eliminating the need for physical impressions.
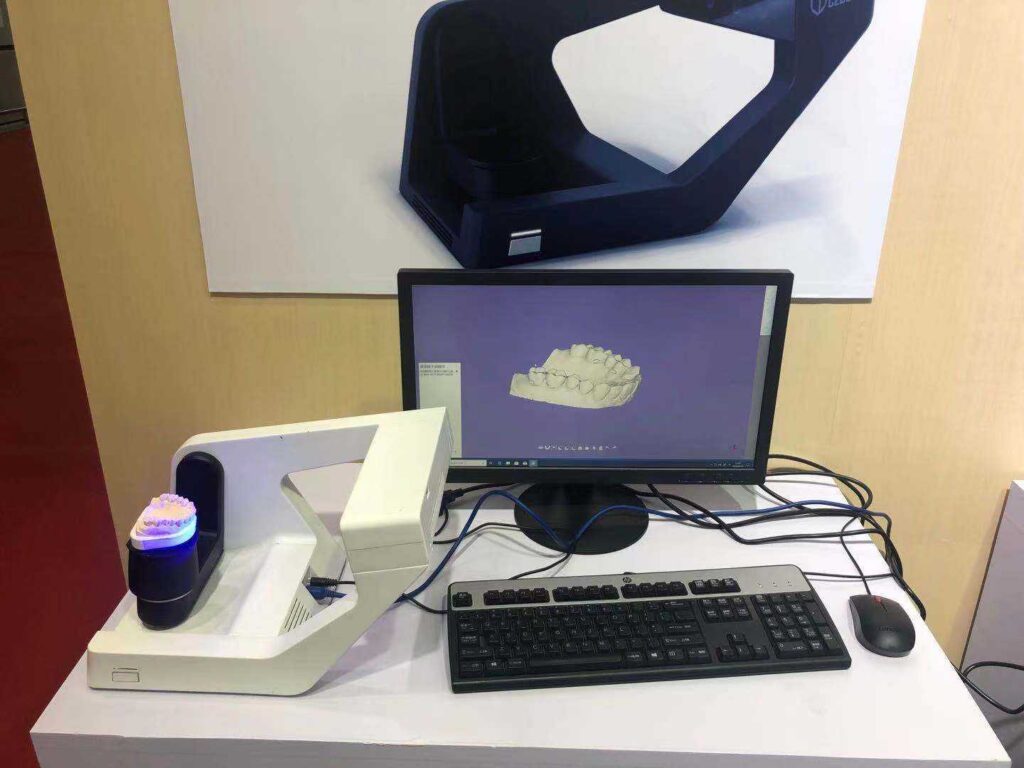
- Digital CAD/CAM Software: Using specialized software, technicians design the prosthetic with precise customization of shape, size, and fit. The software allows for real-time adjustments, ensuring the prosthetic aligns perfectly with the digital model.
- Dry Zirconia Milling Machine: The digital design is sent to a dry zirconia milling machine, which carves the prosthetic from zirconia blocks. This step is ideal for creating durable restorations like crowns and bridges.
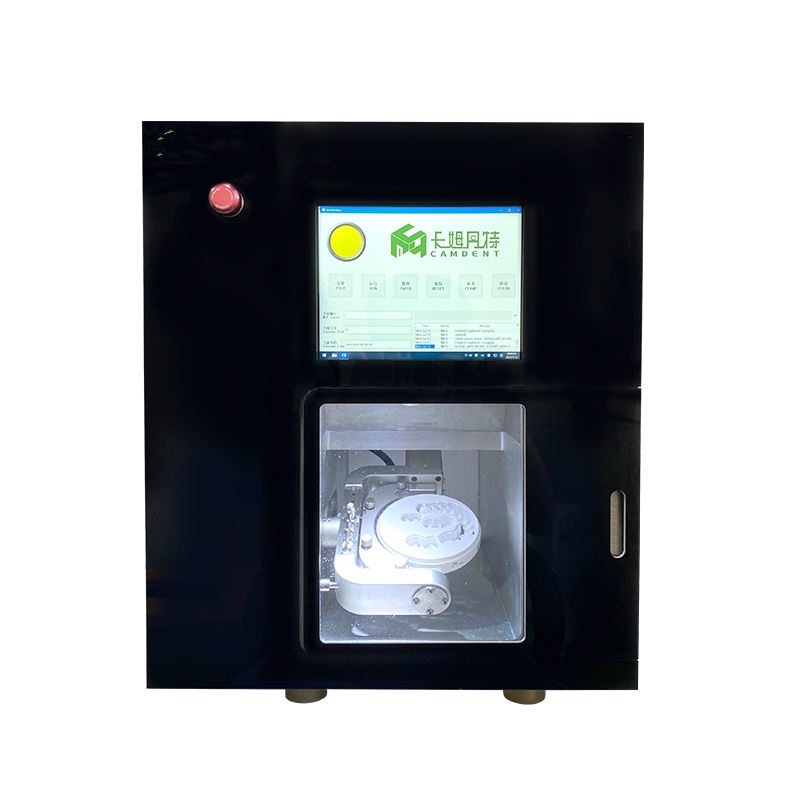
- Wet Metal and Dry Equipment Milling Device: For metal frameworks or other materials, this versatile milling device processes the digital design, ensuring high precision in complex restorations.
- 3D Dental Printer: For specific components or temporary restorations, a 3D dental printer uses dental-specific resins to produce models or patterns based on the digital design.
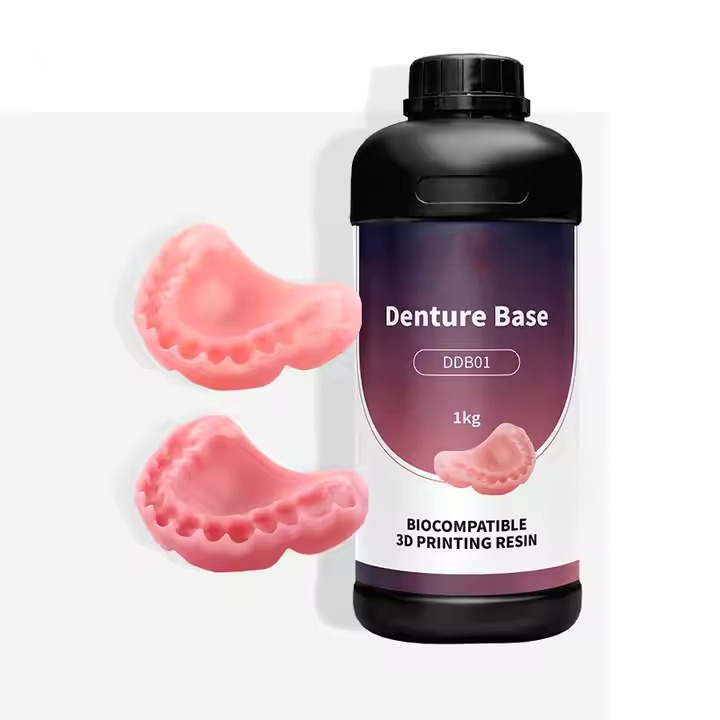
The digital workflow’s advantages are clear: it reduces manual labor, minimizes errors, and accelerates production. Labs can produce prosthetics in hours rather than days, enhancing patient turnaround times. Additionally, the ability to store digital models eliminates the need for physical storage, saving space and resources.
Traditional Casting Manner: A Time-Honored Approach
While the digital workflow dominates modern labs, the traditional casting manner remains relevant for certain applications, particularly when cost or material preferences dictate its use. This method relies on manual craftsmanship and a range of dental lab products to create metal frameworks or flexible dentures. Below is the equipment operation sequence in a clear, structured format:
Step | Equipment | Function |
---|---|---|
1 | Duplicating Machine | Creates accurate replicas of the dental model for use throughout the process. |
2 | Dental Surveyor | Analyzes model orientation to determine the optimal prosthetic insertion path. |
3 | Pindex Dental Machine | Indexes and mounts the model for consistent positioning during fabrication. |
4 | Dental Vacuum Mixer | Mixes investment materials under vacuum to ensure a bubble-free mold. |
5 | Centrifugal Casting Machine | Pours molten metal into the mold using centrifugal force to form components. |
6 | Saw Cutting Machine | Trims the cast metal, removing excess material and sprues. |
7 | High-Speed Grinder | Shapes and refines the cast component, smoothing rough edges. |
8 | Sandblaster Machine | Cleans and roughens the surface for further processing or bonding. |
9 | Electrolytic Polisher | Polishes metal components for a smooth, shiny finish. |
10 | Polishing Lathe | Applies final polishing to enhance appearance and functionality. |
11 | Flexible Denture Injection System | Injects flexible materials into molds for partial dentures. |
12 | Electric Dental Lab Pressure Pot | Cures materials under pressure for dense, durable prosthetics. |
13 | Vibrator | Removes air bubbles during material mixing or pouring. |
14 | Dust Collector | Maintains a clean workspace by collecting debris from grinding and blasting. |
15 | Spot Welder | Joins metal parts, such as clasps, to the prosthetic framework. |
16 | Model Trimmer | Trims the dental model to ensure a proper fit for the prosthetic. |
17 | Vacuum Former Heater | Heats thermoplastic sheets for custom trays or appliances. |
The traditional casting method, while effective, is labor-intensive and time-consuming. It requires skilled technicians to operate multiple machines and perform manual adjustments, increasing the risk of human error. However, it remains a cost-effective option for labs with limited access to digital infrastructure or when working with specific materials.
Comparing the Two Workflows
The digital CAD/CAM workflow excels in precision, speed, and scalability. It reduces the dependency on manual skills and allows labs to handle high volumes of cases efficiently. In contrast, the traditional casting manner is more hands-on, offering flexibility for unique cases but requiring more time and expertise. Labs often combine both methods, using digital tools for design and milling while employing casting for specific metal frameworks.
For modern labs, investing in digital dental lab products is a game-changer. The ability to produce prosthetics with minimal waste and maximum accuracy aligns with the industry’s push toward digitization. However, traditional equipment still holds value, particularly for labs transitioning to digital workflows or serving niche markets.
Looking for these essential devices? Visit Dental Lab Shop for top-tier dental lab products, no furniture required!
Conclusion
The fabrication of prostheses has evolved dramatically, with the digital CAD/CAM workflow leading the charge for its precision and efficiency. While the traditional casting manner remains a viable option, its labor-intensive nature makes it less competitive in high-volume settings. By understanding the equipment operation sequences for both methods, dental labs can make informed decisions about their workflows. Whether you’re embracing the future with digital tools or relying on the craftsmanship of casting, the right dental lab products are key to delivering exceptional prostheses.